Not sure how to account for the amount of work all ready spent on the project.
Probably there is no way other than estimating it and making up a rough
number. So for the sake of doing it, first time welder sparked was May 2004
till today its roughly over 10 years. Light estimate that's 52 weeks over 10
years and an average 3-5 hours per saturday and sunday and taking 4
hours average. mind you some days where much longer and worked during
during the weekdays or did not worked some weekends. In either
case to properly estimate on the hours will be hard to calculate now.
So before it goes too far and to keep track of what was done moving
forward each
time and how its best to start a short diary of progress of each day.
2014-06-19
3.5hr
Have not kept any time line or work log of how things where started, done and
time spent on the project. After many, many years time has come to start
putting some words down on various aspects of the build.
With so many items already completed and endless that have not had been
started and those that are in progress.
Shifter knob for the Porsche gear shifter is endless pain, the plug cracked
again. Plaster is too wet and I keep on making same mistake of not
letting it dry. Needless to say I patched it up AGAIN and poured another
cylinder just in case so I will have to on the go. Maybe just maybe I may
have 2 and I can make up different profiles and sizes for comparison.
Rear light bucks are finally finished and I can make up lenses for it. I'll
have to stop by plastic shop and see if I can find some material for the
lens. Not sure if I should go with tinted or red lens and if I should put a
strip on top to back lit the wing. Back end of the plugs still has to have
some re-leave cut out so that water can drip through and have some provision
for wire feeding and mounting.
Adjusted top of dash instrument cluster, it not has much lower profile and
will not stick up above the steering wheel. Will have to still look into
smaller diameter of steering wheel and hopefully gain some knee space.
Lastly, I had re-welded left rear trunk hinge, moving it by about 1/8 of an
inch. Its not much but with 4 foot long deck it makes a lot of difference at
the end. Now its perfectly centered at the rear even though I will have to do
some adjusting to fiberglass.
2014-06-20 3hr
Did some work on the site cleaning it up and updating.
2014-06-21 1hr
Did a very rough shaping of the 3rd knob cylinder. Man O man I was off on this
one. there was huge corner missing on top and had to add up some more plaster.
2014-06-22 2hr
weekend was pretty much a bust with family life. Good thing though was that it
was 28'C so I left the 2 knobs in the sun to dry. Had a short time at it tonight
and it seems like the sun did the trick. Plaster is much tougher and does not
break as easy though its bit harder to shave it but they turned out great and
both seem to be in one piece so far. Knock on wood and both will make it to
finish line.
So far I have my original knob that now the center is filled and is almost ready
to go and most likely I will use it as test mule for making mold. Second and 3rd
knobs with slightly different over all profile where the 3rd needs more drying
time and moth needs to have final finish done to the top and cavity carved out.
2014-07-16 3hr
Got some time to work on the car again. Did some more work on the dash and
plastered firewall facing mounting side of the dash so that it will have surface
to bolt through into the firewall and also the step-up for display and vents.
Looking at it might be better to have a smoother transition going up where the
part with display will either be part of the top cover or be simply smooth and
forgo the display all together.
2014-07-09 4hr
Worked on dash today, decided to change the way the snap panel around
windshield will
work.
Original idea was to have a cover panel snapped in place on top of a step in
the dash as illustrated in the to the left.
Thought behind the step was to have defroster vents on top with vents in
vertical fascia for occupant comfort and to sides for side window vents. Also
in the vertical space warning lights and or digital readouts can be installed
for extra data display like clocks / temperature or other alpha displays. The
new approach is the best way of doing it as it will give a nice way of
covering the dash and finish edge for material around the snap cover. The
snap cover can have a smooth transition to the glass as first picture below
that would just have defroster vents and has option for a stepped cover in
second picture.
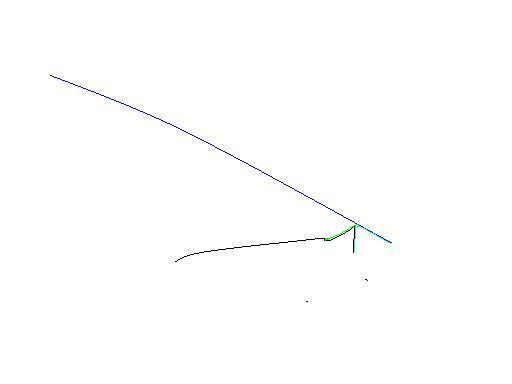
Dash with a smooth snap in panel in to cover mounting screws/bolts.
Stepped snap in cover in green by window covering mounting
bolts/screws. The vertical case can have vents directed as persons face and
or side windows and can also house warning lights or any other digital
displays i.e.. clock temperature displays.
The new area as it was just reworked needs to have symmetrical grove
marked and carved out and the new surface needs to be smoothed out with
mounting surfaces measured and made in a way that the fiberglass structure
will be strong but would not require very long fasteners. Also it needs to be
dished out to house any optional back lighting or display and electronics.
Did a bit more machining on front lower control arm bracket to adapt and hold
both air spring and shock
2014-07-13 2hr
Good start but what a waste of time last time. Had to almost remove half of
what I had done last time, thought it was necessary first step in making the
new provision for the new snap cover. Made provisions for mounting fasteners
(bolts/screws) in front of the dash. Recessed middle part of the snap cover
area to make space for possible indicators and on front corners
virtually cleared out 8" of under snap area all the way to mounting surface
and recovered the new exposed foam with clay.
2014-07-17 3hr
Put couple more hours in today. Cleaned up extra clay around the dash plug
and mudded bit more. I think it finally starting to look as I had it planned.
Will see when its cleaned up next time.
Next big thing. Front suspension more specifically adapters for lower control
arms. The Corvette C5 has single transverse leaf spring perching on the lower
arm with shocks mounted to it. The problem is that I'm planning on using air
bags for main suspension, they do have manual adjustable shocks in them but I
want to add magnetic shocks and that's where the problem is. I want to use
stock A arms in front and OEM only has provision for one or the other. So I'm
trying to make some sort of adapter that I can mount the spring with magnetic
shocks inboard. I have working theory but the actual part needs to be made.
Basically it will be a plate with welded taps running at 90' and mounting
hole for the spring then additional tabs welded to it on 90' and parallel to the
plate so that it can be bolted to the control arm. At the end it will have
stand off's where OEM shock can be bolted to.
Made the main plate today after bit of template trial and error drawing it.
Sketched up the 4 tabs and made 4 stand offs
2014-07-18 4hr
First thing first, check the dash, cleaned up any extra stuff and sanded down
a bit. Some of the plaster is still not quite dry. This thing will work
perfectly, just need to recess a bit the 4 spots where the bolts will go
through for mounting it at the firewall side. I was thinking of clearing out
some of how the lip is made so later it could be easier to route vent hoses
through for defroster. Will see when it cured better.
Cut out the 4 tabs for the front adapters. After bit of adjusting spot welded
the thing up, it will be a beauty .... when its done. Not sure on the
left/driver side, the brake booster might be in a way a bit. DAMN the car is
way to low and its not as easy to squash everything in as in normal 6 foot
tall truck.
2014-07-20 5 hr
Just touched the dash enough to clean up some clay bugers and did a light
coat of fresh plaster. Welded up more like tacked the left adapter. The
freaken shock will be right up the brake booster. Not sure if I should
re-adjust the cross beam more mounting outward to clear more or just forget
the mag shock all together. Before making more decisions I need to get the
rubber top bushing for it. Switching area before making mess. Took engine
cover off and started to figure out mounting tabs for rear springs and
shocks. Those 9000 series springs look rather wide and have very tight fit,
they will probably work, worst case I'll have to go to 8000 series. I'll have
to get air valves now.
2014-07-22
3hr
Made a template and cut out 2 upper spring mounts
2014-07-23 3hr
Made up 2 side supports on back beck to strengthen hinge plates. carved out
deeper indentations in the dash plug for mounting bolts
2014-07-26 3hr
Headlight buckets version 2.0 made up supporting frames for front headlight
buckets with a recessed 1 3/4" driving light . Original buck had both
driving and night light on same plane and it did not looked good with the
little one protruding through the lens. This version makes the light
closer to the wheel so no more 19" rims but the overall look is much
better looking. Both projectors will also be bit lower eliminating pop up bug
eyes. As a bonus I'll be able to probably put eye lid type led surrounds as
marker light and turn indicator. Put down first layer of plaster to get initial
form for the buckets
2014-07-27 2hr
Extended left bucket to outer edge of the fender. Put down extra plaster to
thicken up the buckets.
2014-07-28 3hr
Trimmed down some of the excess plaster from front buckets and roughly
shaped reflectors. Shaped the 4 mounting dimples in the dash. Put
steering column cover back on and adjusted foam around the column.
2014-07-30 1hr
Cleaned up has mounting along side front firewall
2014-08-01 3hr
Did some minor sanding on dash. Roughly shaped front cold air brake split to
add some decorative piece to the front plus it may have a led marker light
embedded later and covered with lens. Made up templates for holes necessary
to mount projectors into front buckets and roughly made 2 holes in the bucket
plug. Had to stop as the clay was still wet inside plus bottom was getting to
thin and was afraid that it would split into pieces. made up 3/4" flat
piece of plaster so that once it dries up it will be fastened to bottom of
the projector.
2014-09-07 4hr
After some family time and vacation I had some time to spend some time and
try to make some progress. The entire summer has been making more part plugs
and this was no exception though it would be nice to move along on the
chassis/body part. Never the less its still been productive. Made some more
progress on the front headlight buckets. I think I finally got what I was
after, lenses might be bit bulged out more then what I would like to but they
still will be following fender lines fairly closely but had to make them bit
higher then what the current fenders are now. I have to remake the fenders
anyway to make one piece that included the front part of the door sill and
lower wheel arch as the pluig was made using same size for front and back
wheels diameter then what will be used so there is a huge gap in the fronts.
Secondly raising light buckets and dropping the arches will make the fenders
look longer which now look kind of short. One sight problem is that the
bumper will need to be adjusted slightly where it will have to be cut down to
clear the larger projectors bringing the cut line to the original line where
it was planned on and will have to cut some of the fibre glass and re-fill
it.
Sep 21, 2014 2 hr
Did some sanding on the left headlight bucket. Got it to a point where its
almost same shape as the right. Unfortunate part is that the small
projector is off by quarter inch so I had to refill it on one side and leave
it alone to dry
Sep 25, 2014
Picked up 4x8x0.125 aluminum plate to make up fuel tank. Once the tank is
done the center tonou and floor can be finished.
Oct 4, 2014 2hr
Not much time in garage. The instrument cluster was bugging me for some time
from the first day it was made. It was way too tall and sticked out above the
steering wheel where it obstructed vision of the road just ahead of the
bumper. Decided to flaten it out as result it shrunk down and it looks like
its bit wider then it was. However it does give a better view.
Oct 12, 2014 4hr
So I got another few hours in garage. getting closer to getting shape of
headlights, trimmed down and got upper contour of the headlight almost where
I wanted to originally be at. Still need to do a lot fine tuning to the
contour though. Will have to reshape bit further inner center part and
especially around the smaller projector to get bit more space for trim ring
and figure out how to shape up the turn and driving reflectors housing the
LED's.
More important, finished welding/stitching sheet metal on left and right
sides of the center tonou. have to do some finishing to the welds and smooth
them out as some spots could be better. This had been dragging for a long
time and I'm glad that its finally finished and it looks soo much better.
Need to trim down and finalize shape of the model fuel tank making sure that
it will slip in and out easily from the cavity and make the actual tank. Once
that is done the top part of the tonou can be made closing it off and then
the floor can be welded in.
Oct 18, 2014 2hr
Did a bit more work on the headlights on extending mounting surface for back
weather cover and trying to get a better top curve on the lens. ant to much
more and I think I'll gave to pull the trigger and cut the bumper up to
better fit the headlight in and make final adjustments.
Oct 26, 2014 2hr
Decided to cut out openings for headlight buckets today. With the rough cuts
looks like the headlights will fit perfectly in the fender / bumper. Lower
section of the headlights need some work as they have to be extended due to
the triangular cutouts in the bumper so that the lens will be flash with rest
of the panels.
Added some more material on the headlight buckets to have them extended and
have mounting surface for lens cover. Once they are finished, the cut out area
in the bumper will be re-fibreglassed with spacing between headlight and
bumper then the fenders will be altered to reduce opening in the arch and
wheel and also drop fender height.
Nov 9, 2014 2hr
Readjusted cutouts in the front bumper for headlight buckets. Now they sit
nicely inside with bit extra space for to move the buckets around. As the
fenders have to be remade not sure if I should leave the buckets as plugs and
work on the fenders or make the molds and pull parts out .
Nov 29, 2014 4hr
One of the better days for this final days of fall. Changed the way front
trunk upper and cross tubes had been done, they had been bugging me for long
time with the opening on sides and small support pieces in the middle. Cut
out 2x2 tubes and
re-welded new pieces in their place properly oriented. Also welded in the cross support bar to
hold the windshield surround in. Decided to also weld in the back trunk sheet
metal covering steering rack and what not to be in the place, looking at it
not sure how the windshield wiper regulator will fit there now.
With tabs welded in the center tonou for bolts to cover up the fuel tank,
fitter the mockup of fuel tank in place. Looks like I need to make some
adjustments to it :-/ there are some clearances issues in couple spots
around bends where it narrows down from back going forward on top and need to
narrow it pretty much on the entire bottom plane. Well that bites a bit
as it will reduce tank capacity by couple of liters.
What can ya do !!!
Nov 30, 2014 5hr
Another great day !!! Touched up on some unfinished welding spots,
finished welding up passenger sill plate. Ground down a lot of welds on the
right side, she is almost ready on that side aside from extra mounting points
for anything that goes back and forth. Might have to weld up some bolt tabs
on the outside too to hold up cover plate making the side nice and smooth
once completed.
Trimmed and tacked back in center sheet metal on rear firewall to hold the
rear window regulator. I hope I dont need to have that section open trying to
finish something, but it does make the firewall more completed.
:-( the cross bar on front firewall holding the windshield I welded in is too
long and can not put brake booster and bolt it in place. Had to remove
2 inches from the length and may need to remove another 1" to properly
clear it. Will have to see how will that work next time. Never the less that
piece of sheet metal is tacked in and hopefully I will not need to remove it
when making other adjustments there as I started making corner filler sheet
metal pieces to close off and only thing that will be left is the floor in
the trunk area.
Dec 6, 2014 4hr
Short but good day again. Made a second piece of right corner filler for the
trunk and weld it in and made the 3rd filler plate and tacked in place. Left side is next, have the bottom filler made.
Will need to trim down on brake booster opening and make up upper part.
Dec 8, 2014 2hr
Welded in lower part of the left trunk corner and made a bit better clearing
so that the brake booster can be removed. Started making templates for rest
of the upper rear left trunk corner as it needs to be different as not to
make odd looking shapes and indentations.
Dec 9, 2014 1.5hr
Spent some time making up cardboard template for the left trunk corner. Need
to cut some small piece of sheet metal out to make the transitions bit
smoother but it looks like it will not have huge protrusions when all is
done. Amazingly the folded up template can be made out of single flat sheet
of metal. Interesting part will be how to bend the sheet metal with all the
folds weldup tabs.
Dec 11, 2014 4.5hr
Cut out a sheet metal to the size of the trunk upper left corner template.
There is one fold that goes across entire sheet, which helps a lot in bending
it. Amazingly rest of the fold went soo much easier then anticipated. Prepped
the area in the trunk and tacked in the sheet metal. After bit of trimming
the corner was tacked in for short inspection of how it will fit it was
tacked in and fully bud welded as to prevent any liquid penetration. The
welds were ground down to dress them up then everything was primed.
Excess sheet metal on top was marked and trimmed.
Dec 17, 2014 1.5hr
Looked around to see how to setup mounts for the magnetic shocks in the front.
Its not going to be easy. The OEM shocks are about 4” too long if our
retrofit idea to be used in order to clear the brake booster on driver side.
On passenger side its not as bad as the upper mount could be moved up and
inwards to clear the frame rail. The option is just to use the air springs
with built in dampers.
Dec 19, 2014 6.5
Had day off today. Trimmed down the windshield fiberglass surround to clear
the extended box for brake booster. Looks like body work is delayed one more year,
not necessarily bad as a lot of plugs are in the process of being worked on
and some of the body panels being adjusted as the chassis is still being
finished.
Did a lot of work around the magnetic shocks, looks like the only way is to
make custom lower A arm and not using the OEM C5 arm, upper arm is unaffected.
In order to use the magnetic shocks lower arm will need to have lower mount
for the shocks protruded about 2” below the arm. On positive side is that
proper mounts can be fabricated for the air bag and the magnetic shock.
Made up plates and tabs that will be welded to the upper A arm bar to facilitate
mounting of the magnetic shock. Next time I can set them up and weld them up
together and into the frame.
Dec 21, 2014, 3hr
Had a good day in garage again :). Finished welding up front shock perches,
cleaned them and welded them onto the frame and covered them with anti
corrosion primer. Still need to figure out how to make the wiper regulator,
drill and tap holes for upper trunk ledge and weldup tabs for ride heigth
sensors when its back on the ground
Total 94 hr
Thats it for this year, on to 2015
|