With body being made out of multiple panels, we needed them to be easy removable
for maintenance of replacement n case of accident. Therefore the mounting needed
to be done with bolts rather then bonding method or welded onto the frame with
embedded metal pieces into the panels.
With the exception of the windshield frame/surround / and A pillar which is
bonded onto the windshield frame A pillar sub frame with poly urethane. All
remaining panels are bolted directly to the chassis. In order to do
that the chassis was made in a way that strategically located mounting tabs and
weld in nuts into the chassis tubes are virtually leaning against the panels.
There small gaps left to either fill in with fiberglass filler to compensate for
variations in panel thicknesses or just to have a smooth surface to mate against
a tube when then was cushioned with rubber as anti-vibration or make it water
tight.
With the panels being bolted directly onto the chassis, the added benefit was
that all of the chassis tubes where able to be pushed as far out as possible
thus providing biggest possible
space for creature comfort plus making as much space as possible to the systems.
Panel to chassis mounting
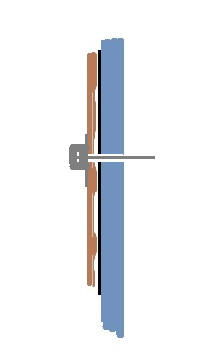
Picture to the left shows off typical panel to tube mounting with welded in rod
that is drilled through and tapped to receive a mounting bolt illustrated by the
thick blue line.
The brown line is a body panel, flat on outside and surface variation towards
the tube.
white void is area filled in with filler making part of the body panel
The black line is the rubber or foam membrane that prevents squeaking and makes
water tight
Gray is a bolt with oversized washer against the fiberglass preventing
possible cracks in the panel.
Similar process is applied to panels that are bolted to a tab rather then a tube
but over a smaller area of the body panel
Panel to Panel mounting
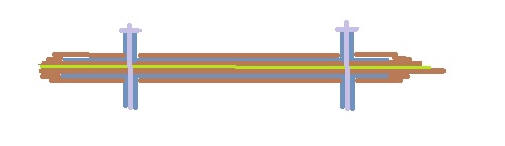
Panel to panel mounting are bit different of how they are mounted or
bolted together.
Main reason for doing so is that there is no chassis that the panels or
joints between the panels that could be bolted to.
The panels have fiber glassed in metal standoffs on each panel directly facing
each other. Those stand offs are also welded into a sheet metal which painted to
prevent rusting. One side is over drilled so that bolt would thigtly fit into
the hole and other stand off is threaded. So by having 2 or more of this type of
stand offs that are bolted together provides ridgity to the mounting from
vibrating or moving around. From picture above the yellow line is the gel coat
or paint that's on the panel. In blue is the sheet metal and stand offs
that are fiber glassed in and represented by the brown area.
One of the mounts is between rocker and quarter panels. The panel joints are of
triangular shape and having 3 bolts. This way the panels can not bowl or twist
and thus not making the contour of the body to change.
Second place where this type of joint is used is with lower diffuser. However in
this case the diffuser is bolted to the chassis. Then lower part of quarter
panels are then bolted with 2 bolts on each side to the diffuser. In this
situation, with diffuser being mounted to the chassis prevents moving sideways
and having 2 bolts on the sides prevents the diffuser and in a way quarter
panels from sagin beging the rear wheel
... More Content Coming Soon
Panel bonding (windshield frame)
There is only one body part that is bonded to a frame and that's the windshield
frame it self. As the windshield frame and A pillars are one unit and made
to me removable by removing few bolts that are used to fasten it to the main
chassis. It is possible to have the windshield frame and body panel bonded to
each other.
... more content coming soon
Panel frame reinforcement
With some larger panels like engine lid, front trunk, doors and roof there is a
metal frame that is bonded into the body component doors specifically or
sandwiched between 2 fiberglass panels. The metal frame adds mounting points
for bolts and also provides re-inforcment to the large fiberglass panel.
... more content
coming soon |